Opening the Power of Welding WPS: Approaches for Performance and Safety And Security in Manufacture
In the world of construction, Welding Procedure Specs (WPS) stand as the backbone of welding operations, determining the essential actions for accomplishing both performance and safety and security in the manufacture procedure. Comprehending the complexities of WPS is critical to harnessing its full possibility, yet several companies have a hard time to unlock real power that lies within these records (welding WPS). By diving into the strategies that maximize welding WPS, a globe of improved productivity and enhanced security awaits those happy to discover the subtleties of this important facet of manufacture

Value of Welding WPS
The significance of Welding Treatment Requirements (WPS) in the construction industry can not be overemphasized. WPS act as an essential roadmap that details the required actions to make sure welds are performed continually and properly. By defining necessary parameters such as welding processes, materials, joint styles, preheat temperatures, interpass temperature levels, filler metals, and post-weld warmth treatment needs, WPS offer a standard method to welding that boosts effectiveness, top quality, and security in manufacture processes.
Adherence to WPS aids in achieving harmony in weld quality, minimizing the likelihood of flaws or architectural failures. This standardization additionally facilitates conformity with sector policies and codes, making certain that fabricated structures fulfill the required security criteria. Furthermore, WPS paperwork makes it possible for welders to replicate effective welding procedures, causing regular results across various tasks.
In essence, the precise advancement and stringent adherence to Welding Procedure Specs are vital for promoting the honesty of bonded structures, protecting against possible hazards, and supporting the credibility of fabrication business for supplying high-quality services and products.
Secret Components of Welding WPS
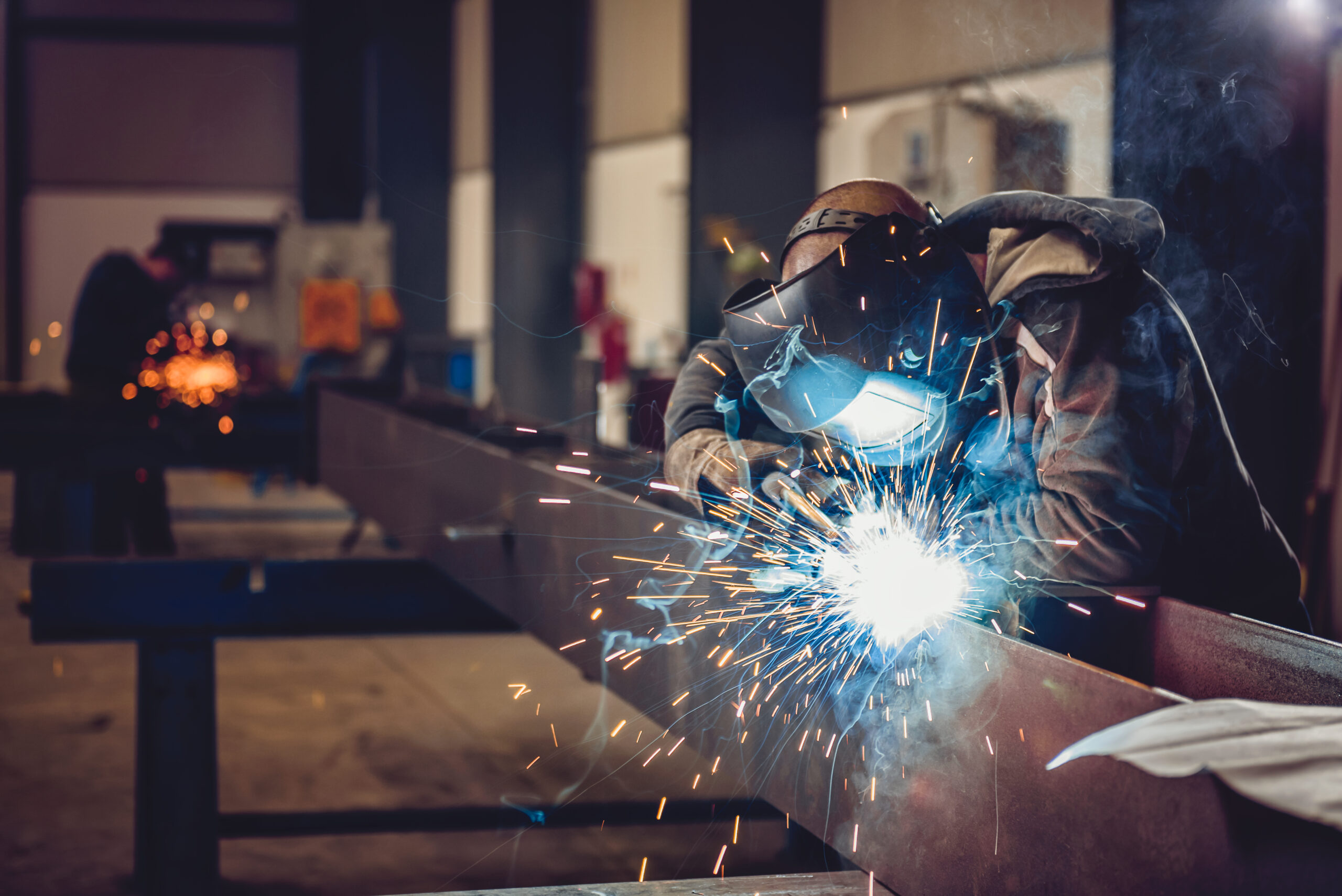
Enhancing Efficiency With WPS
When optimizing welding operations, leveraging the crucial elements detailed in Welding Treatment Specs (WPS) comes to be essential for improving processes and taking full advantage of performance. One means to boost effectiveness with WPS is by very carefully choosing the proper welding specifications. By adhering to the particular guidelines provided in the WPS, welders can ensure that the welding equipment is established appropriately, bring about top notch and constant welds. Furthermore, following the pre-approved welding sequences described in the WPS can dramatically decrease the time invested on each weld, eventually enhancing overall productivity.
Frequently reviewing and upgrading the WPS to include any lessons discovered or technical innovations can also contribute to effectiveness renovations in welding operations. By embracing the standards established forth in the WPS and continually seeking ways to enhance procedures, makers can achieve higher efficiency levels and premium end results.
Ensuring Safety And Security in Manufacture
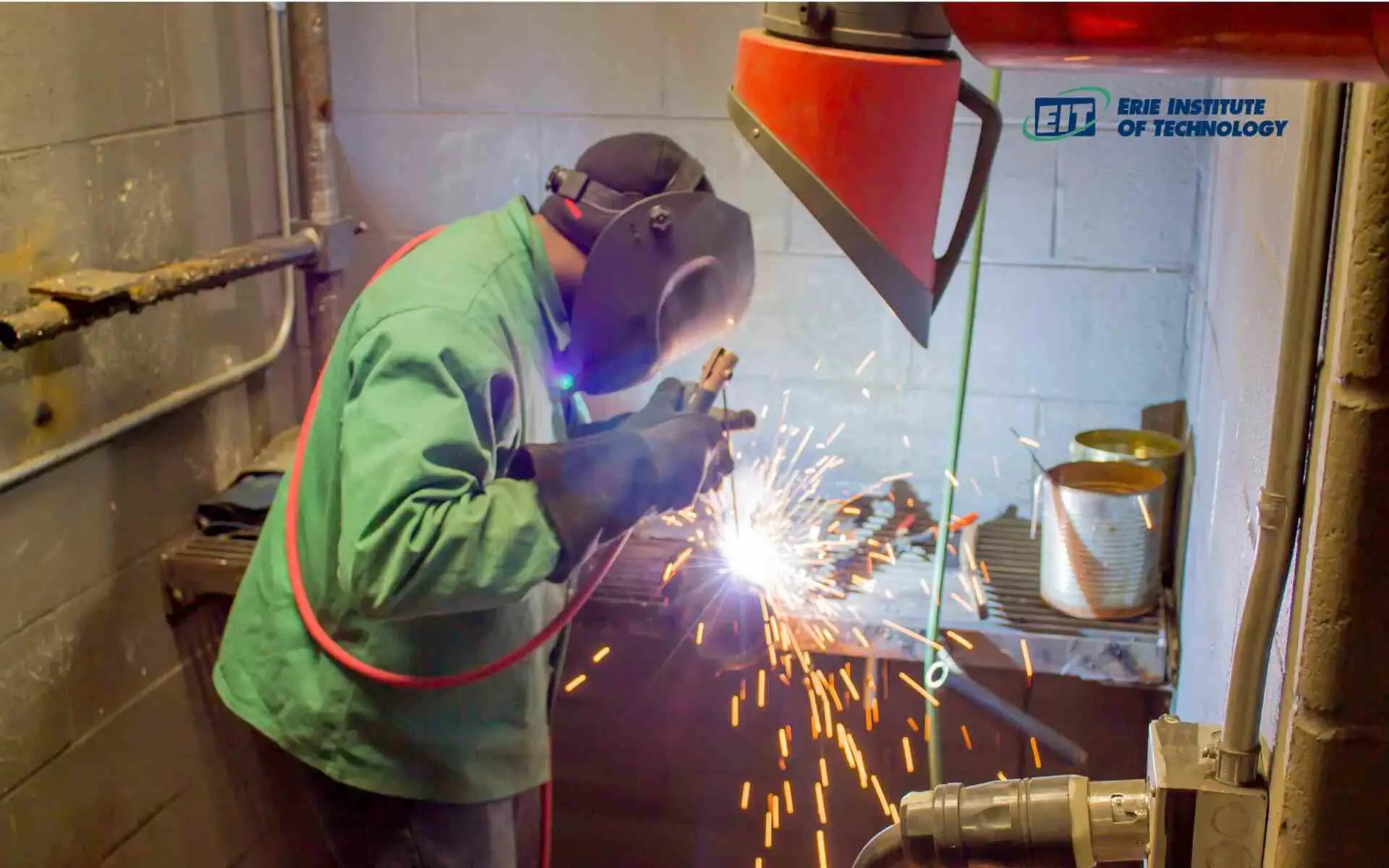
Safety methods in manufacture play a pivotal role in safeguarding personnel and maximizing functional procedures. Ensuring safety and security in manufacture includes a multifaceted approach that incorporates different aspects of the welding procedure. One essential aspect is the stipulation of individual protective tools (PPE) tailored to the specific risks existing in the construction atmosphere. Welders must be furnished with suitable equipment web such as safety helmets, gloves, and safety clothes to mitigate dangers connected with welding tasks.
In addition, adherence to appropriate air flow and fume extraction systems is vital in maintaining a healthy and balanced workplace. Welding fumes have hazardous materials that, if inhaled, can present significant health dangers. Implementing efficient air flow measures assists to lessen exposure to these dangerous fumes, advertising respiratory system health amongst employees.
Regular equipment upkeep and examinations are also vital for making certain security in manufacture. Malfunctioning machinery can lead to mishaps and injuries, emphasizing the importance of prompt fixings and routine checks. By prioritizing safety and security measures and fostering a society of recognition, manufacture facilities can create a efficient and safe job dig this setting for their employees.
Applying WPS Best Practices
To enhance operational efficiency and guarantee high quality results in construction processes, integrating Welding Procedure Specification (WPS) best practices is critical - welding WPS. Executing WPS best practices involves meticulous planning, adherence to sector criteria, and continual surveillance to ensure ideal results. Firstly, picking the ideal welding procedure, filler product, and preheat temperature level defined in the WPS is vital for accomplishing the preferred weld quality. Secondly, making certain that certified welders with the needed accreditations execute the welding procedures according to the WPS standards is necessary for consistency and reliability. Regularly reviewing and upgrading WPS records to show any type of process renovations or modifications in materials is additionally an essential best technique to preserve accuracy and importance. Furthermore, providing comprehensive training to welding workers on WPS requirements and finest methods promotes a society of safety and top quality within the construction atmosphere. By diligently executing WPS ideal methods, fabricators can enhance their operations, lessen errors, and supply superior items to meet customer expectations.
Verdict
Finally, welding WPS plays a vital duty in guaranteeing effectiveness and safety and security in fabrication processes. By concentrating on vital elements, enhancing effectiveness, and implementing finest practices, firms can enhance their welding procedures. It is important to prioritize precaution to stop mishaps and make sure a smooth manufacturing procedure. By adhering to these strategies, companies can unlock the full capacity of welding WPS in their construction procedures.
In the world of construction, Welding Procedure Specs (WPS) stand as the backbone you can try this out of welding operations, dictating the essential actions for attaining both performance and security in the construction process. By defining essential parameters such as welding procedures, products, joint styles, preheat temperatures, interpass temperatures, filler steels, and post-weld warmth treatment requirements, WPS provide a standard strategy to welding that improves effectiveness, quality, and safety in manufacture processes.

When optimizing welding procedures, leveraging the vital aspects described in Welding Procedure Requirements (WPS) comes to be essential for taking full advantage of and streamlining procedures efficiency. (welding WPS)